When an organization examines its position in a global marketplace, the competition for customers can be brutal. Customers look for suppliers who will provide the greatest value for the money. The value equation can have a number of components including:
- Fair Pricing
- Impeccable Quality
- On-Time -Delivery
- Responsiveness
- Outstanding Reputation
- Expertise
An organization has to evaluate the value it generates from the perspective of their customers. The value stream within an organization includes everything from getting the order to delivering the product or service and getting paid. This value stream crosses all of the functional areas that define the organizational structure of the company.
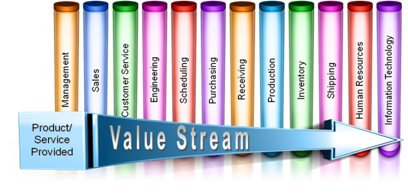
In establishing the price charged for the product or service provided, the
Total Cost to produce that product or service must be considered. An often overlooked cost component comes from the non-production areas like the office.
Today, enormous amounts of waste exist in office and service environments. Delays, bottlenecks, errors, redundancy, and work-arounds are very common. Non-value added work can be as high as 70 percent. A proven "people-oriented" approach that can help reduce or eliminate these wastes while streamlining value-added activities is what Lean Office is all about.
Taiichi Ohno, a former Chief Engineer at Toyota, developed a list of “Seven Wastes” that add cost but no value to the product or service provided to the customer. Later an eighth waste, Unused Employee Creativity, was added. The following represents an adoption of these wastes for office and service areas and can be used as a starting point in the identification and elimination of office waste.
WASTE |
DEFINITION |
EXAMPLES |
Overproduction |
Producing more work, sooner or faster than is required by the next process |
- Processing/printing paperwork before it is needed
- Documents being processed in large batches
- Reports not used or read
- Unnecessary e-mails
|
Touches |
Unnecessary "touches" of work (paperwork or electronic information) |
- Stocking supplies far from their point-of-use
- Moving manual and electronic files in and out of storage
- People in different locations requiring constant communication (virtual meetings, E-mails)
- Multiple hand-offs, multiple approvals
|
Unnecessary Motion |
Unnecessary movement of people |
- Searching for documents in file cabinets and in computers (too many layers for E-folders in computer)
- Ineffective layout of office area
- Copy/fax machine (printer) too far away from users
- Lack of centralized office equipment/filing
|
Waiting |
Any delay between when one process step/activity ends and the next step/activity begins |
- Meetings starting or ending late
- Late reports and projects
- Waiting for signatures and approvals
- Computer system down, slow system response time
|
Overprocessing |
Trying to add more value to a service/product than what your customer will pay for |
- Too many approval levels
- Endless refinement (work to get 1 percent accuracy when customers are fine with 10 percent)
- Too many steps to complete a task
- Re-entering data, extra copies, excessive reports
|
Excess Inventory |
Any work-in-process that is in excess of what is required to make for the customer |
- Stagnated documentation between processes
- Duplicate forms to do the same thing
- Completely filled “In-boxes” (electronic and paper)
- Backlog of work that no one has time to do
|
Defects |
Any mistake, rework or workaround that occurs in meeting customer needs |
- Missing information
- Lack of standardized work, excessive inspection
- Incomplete requirement specification
- Incorrectly entered customer data
|
Unused Employee Creativity |
Losing ideas by not engaging or listening to employees |
- Employees do not know the Eight wastes
- No communicated strategy for continuous improvement
- No formal suggestion process in place to solicit ideas
- Unclear job descriptions
|
These wastes exist and are adding non-value-added cost to the organization. The result is decreased pricing flexibility with customers who, because of the internet, are better informed and have easy access to suppliers around the world. Competing in this environment requires companies to constantly find and eliminate the waste in their processes. The cost of waste can no longer just be passed on to the customer in higher prices.
While the fundamentals of Lean are somewhat intuitive, many of the most successful components of the “Lean Office Toolbox” have been developed over many years. Providing the right set of skills to people, allows your organization to quickly learn these tools and realize the benefits of Lean Office without expensive trial and error. Embarking upon a lean journey that includes the office activities will contribute to the profitability and competitiveness of the organization by improving the value delivered to your customers.