World-Class!
What does that mean? In simple terms it means that an organization is operating at the highest levels of performance and is considered to be one of the best in the world, in the sectors in which they compete. These performance levels are verified through benchmarking studies of other organizations within the sector.
Before a company can talk about being world-class, they have to build an organization that has the foundation, structure, and systems, which makes it possible to compete with the best organizations in a constantly changing global marketplace.
As you begin the strategic management process to define your world-class organization, five major tasks are involved:
- Developing a strategic vision and business mission
- Setting strategic objectives
- Creating a strategy to achieve the strategic objectives
- Implementing and executing the strategy
- Evaluating performance
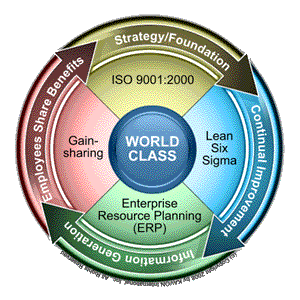
This article, will explore an approach to creating, implementing, and executing the strategy by building the foundational systems, which position an organization to compete with the best in the world. These systems include:
- ISO 9001:2000
- Lean/Six Sigma
- Enterprise Resource Planning (ERP)
- Gainsharing System
ISO 9001:2000
An ISO 9001:2000 system, properly implemented and diligently adhered to, can become the cornerstone for a world-class company. The foundation established by this system, brings discipline and documentation to the company culture while focusing on customer satisfaction through continual process improvement. ISO 9001:2000 plays a central role in creating and sustaining customer satisfaction through the elements of quality cost, flexibility, reliability, and innovation.
ISO 9001:2000 provides the foundation on which to build a world-class company. It starts with the Quality Policy and Quality Objectives, which are established to provide a focus that directs the organization. Processes are then established, which define how the organization will achieve its objectives and fulfill its Quality Policy. Controls are put in place, which provide the information and mechanisms that allow the system to monitor and correct problems when they arise. These include management review, internal audits, corrective actions, document control, customer complaints, and customer satisfaction. In addition to the internal audits, an outside third party Registrar periodically checks the system for compliance.
Lean/Six Sigma
The processes defined in your ISO 9001:2000 system have to be continually improved, as required by the standard itself. One of the best ways to accomplish this is through the deployment of Lean/Six Sigma methodologies. Lean looks at your processes with an objective to eliminate waste, which is defined as anything that the customer does not want to pay for. Six Sigma uses methodologies that attack the variation in each process with the goal of eliminating it or at least reducing it to acceptable levels.
Enterprise Resource Planning (ERP)
Part of an effective management system is getting accurate information in a timely manner to make decisions. An ERP system is the solution that takes data and converts it into the information needed to effectively run a business and plan for the future.
An effective ERP system:
- Helps support the ISO 9001:2000 system by providing measurement information on the quality objectives and the effectiveness of the company?s processes.
- Supports the Lean/Six Sigma initiatives by providing benchmark information on the status of your existing systems and processes.
- Documents the gains achieved through successful improvement project implementations.
Gainsharing System
The effectiveness of the ISO 9001:2000 system and the continual improvement gains achieved by the Lean/Six Sigma project teams hinges on the ability of the organization to properly motivate its employees. Employees need to align their work habits with the objectives articulated in the business plan, quality objectives, process measures, and the Lean/Six Sigma project plans. Everybody has to be working toward the same objectives. The goal is to make sure that the reward system directs efforts toward the achievement of the organization?s objectives and mission.
Your Company can be World-Class!
Embrace the structure, documentation, and discipline of ISO 9001:2000 coupled with the process improvement tools of Lean/Six Sigma, the reporting capabilities of ERP, and the employee involvement generated by an effective gainsharing system. This is a recipe that will distinguish your company as a top performer in your industry and will put your company on the road to World-Class.